VAM® Field Service
Our teams of highly trained technicians based around the world are available to help you verify and deploy your connections. Using VFS experts reduces costs, improves operational efficiency and inventory control throughout the lifecycle of your pipes and connections.
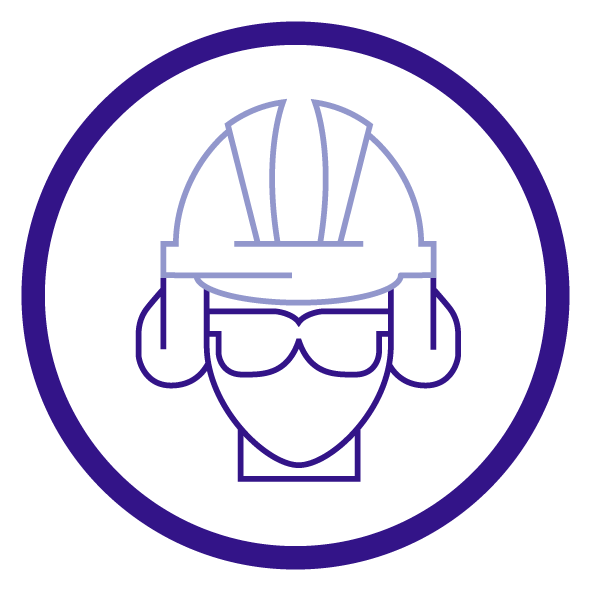
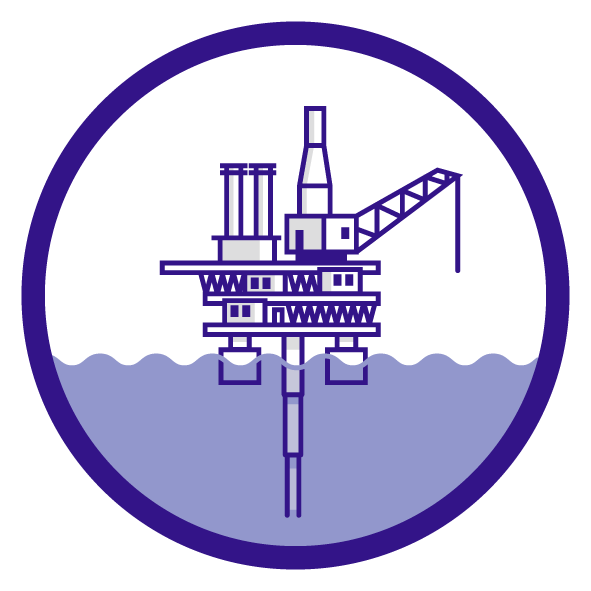
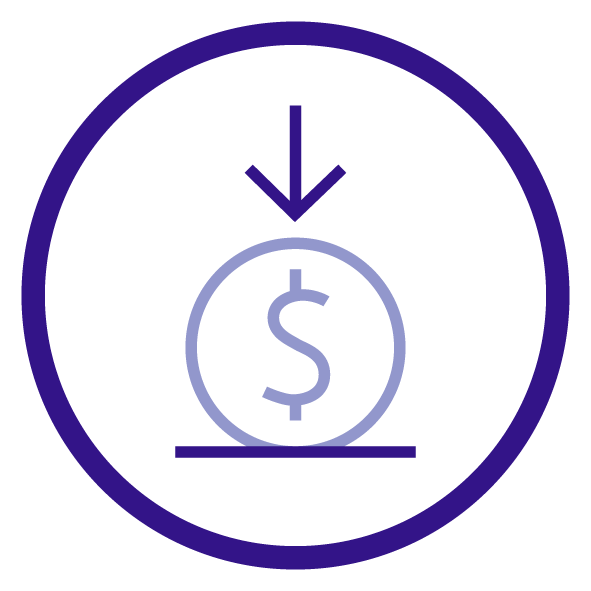
Our 180 highly-skilled technicians are based out of 19 service centers all over the world. Through a range of services from mill to well, VFS guarantees quality and performance for operators using VAM® products.
Tried and Trusted Services
- Rig site services
• Running supervision
• Deck inspection
- Loading/off-loading supervision
- Thread inspections – rig-ready and rig return
- Sub-assembly makeup & repair
• Supervision of assembly make up
• Calibration checks
• Make-up process qualification
• Workshop audits
• Pressure test fixtures rentals
• Pipe repairs coordination
- Pipeyard management
•Digital stockyard management
• Collaborative planning
• QHSE best practices
• Yard design and audits
- Rig preparation
- VAM® Licensees
•Quality control and Licensor Technical Representative for VAM®
Supported by Innovative Tools
- TallyVision
- Data analytics
- Pre-Installed Cable Protector
- Prime Mapping
- Digitalization of Stockyard Management
- Tubular Repurposing
VAM® Field Service Quality Management System
VAM® Field Service is working on the implementation of API Q2 in all our service centers globally.
VAM® Academy
The VAM® Field Service Academy, unique in the industry, trains and assesses engineers.
VAM® Field Service on the rig site
Our expert technicians work on your rig to ensure that the right products are used at running to protect the integrity of your well. With extensive training and experience, they can verify the condition of the products, validate all the make-up parameters and conditions, create conclusive make-up graphs and decide when a connection should be backed out, accepted or laid down. Thanks to their expertise, you can greatly reduce back out and reject rates, helping ensure your well is safe and the connection performance is optimal.
Embedded VAM® technician support
Embedded in your team, a VAM® technician is on-site to ensure things run smoothly. From supervising, reporting and trouble-shooting operations in real time to proving answers to day-to-day questions, having a VAM® technician can help avoid costly mistakes, improve the efficiency of your operations and lower your costs.
Bucking unit qualification and calibration
VFS technicians visit your completion workshop to verify the make-up process meets VAM® requirements for tolerances and processes. They train, assess and test personnel and calibrate the make-up machine to VAM® standards (TSLI 440) with a customized frequency using calibration bars. They also verify the accuracy of the machine’s torque measurement. As an independent third-party, they can confirm the correct calibration of your machines so you can be certain your workshop meets VAM® standards.
VFS Licensor Technical Representative (LTR)
Licensor Technical Representatives (LTR) receive critical parts that are manufactured at VAM® licensee machine shop locations. They offer reliable, local repair and manufacturing of VAM® Connections, even in the most remote locations. Specially trained and highly qualified VAM® Specialists inspect the products to ensure they are fully compliant with VAM® standards. Get the assurance that your locally-manufactured product is VAM®-certified.
Low-torque soft seal pressure test fixture rentals
All VAM® Field Service centers offer rental pressure test fixtures that meet all safety standards. They hold the required test pressure and are truly low-torque. Durable and robust, they can withstand numerous make and breaks. Their design prevents the change of the deformation of the VAM® connection after the test, and they will not damage the connection at make-up or break-out. No transfer of seal galling from the test fixture to the product. Test the integrity of your connections and ensure your operation is efficient.
Make-up graph review
Our team of experts across all time zones offers remote assistance with your make-up graph profiles. They have the knowledge and experience to identify possible root causes of bad profiles and propose corrective actions.
A specific project? Need VAM® Field Service assistance? Let’s talk about it!
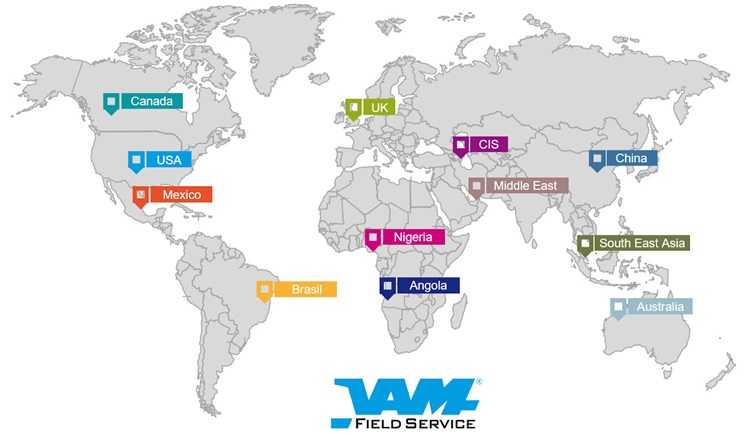
VAM® Field Service Middle East proudly announces its successful achievement of the prestigious API Specification Q2 certification, marking a significant milestone in service quality and operational excellence.
VAM® Field Service (VFS) has now monitored the torque turn of one million feet of OCTG casing with zero safety incidents or downtime for the rig over the past two years. The team’s exceptional performance sets a new standard for operational excellence in the fast-paced oil and gas industry, where safety and efficiency are paramount.
A VFS technician assisted a customer after sub-assembly pressure tests at a third-party workshop resulted in recurring leaks and damaged threads. He audited the workshop, performed the qualification of the horizontal make up unit, supervised the assembly make-up and replaced metal-to-metal TCP with low torque soft seal pressure test fixtures. The result: > zero leaks, > a reduction of costly and repetitive tests and > no need to recut damaged threads.
Discover our solutions
More information