Delphy Hydrogen Storage
Delphy is an innovative underground hydrogen storage system with minimal surface footprint, enhanced safety parameters and a modular design.
The world is in urgent need of transitioning swiftly from a fossil fuel-dependent economy to low-carbon, zero-carbon, and even negative-carbon technologies.
Initially, the shift will involve replacing fossil fuel-derived hydrogen with low-carbon hydrogen generated through the electrolysis of water using renewable energy sources. Industries such as ammonia and steel production exemplify applications where renewable-based hydrogen will supplant fossil-based hydrogen.
Subsequently, various sectors currently reliant on fossil fuels—like mobility, glassmaking, and steel production—will undergo electrification or transition to hydrogen-based technologies.
For instance, industries responsible for significant CO2 emissions, such as mobility encompassing aviation and maritime transport, cement and construction materials, as well as glassmaking and district heating/cooling, will transition from fossil-based technology to electric or hydrogen-based solutions, such as synthetic fuels or fuel cells.
The widespread adoption of these applications necessitates substantial and secure storage of hydrogen.
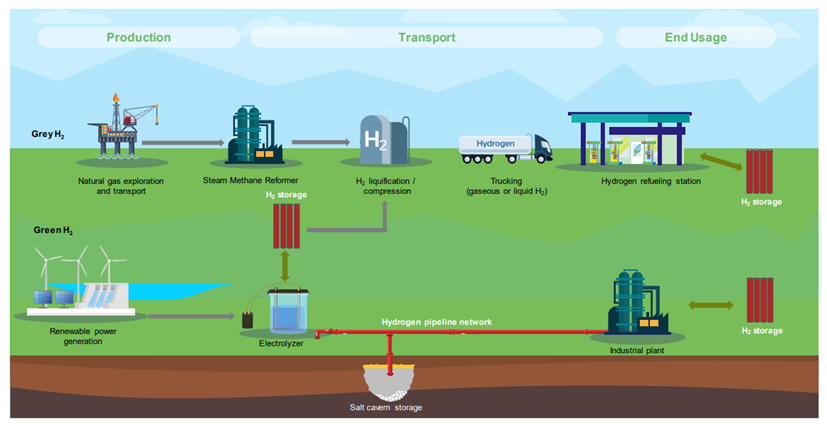
Hydrogen storage can create value along the various stages of the value chain:
Hydrogen production by electrolysis faces issues of variability of electricity availability and price, as hydrogen production often depends on intermittent energy sources. Producers can use hydrogen storage to optimize the electricity mix they use and improve the competitiveness of hydrogen production. Otherwise, they can simply use storage to offer stable output, regardless of the power source’s intermittency.
Midstream steps in the hydrogen chain involve transport and distribution. In many circumstances, this can involve a storage need. This might be the case, for instance, at hydrogen refueling stations (HRS), where a buffer of high-pressure hydrogen is needed to guarantee the refueling of several vehicles consecutively at any time. And the same applies to fill trailers to ship hydrogen from producer to offtakers.
Downstream, the challenges for hydrogen revolve around supply consistency. End users in industries such as shipping and steelmaking require a high degree of continuity and the assurance that hydrogen will be continuously available. A buffer storage will ensure this consistency and can accompany the ramp-up and ramp-down phases of the production regime, in case of unexpected events.
Hydrogen storage poses significant technical hurdles, necessitating innovative solutions. The challenges stem from several root causes, each presenting its own set of issues that Vallourec addresses with precision.
- The low density of hydrogen necessitates high pressure for storage, demanding considerable space, thus impacting the footprint. Vallourec’s response lies in crafting high-pressure solutions that occupy minimal space, optimizing storage without compromising efficiency.
- Hydrogen’s small molecular size makes it prone to leakage, posing a challenge for containment. Vallourec counters this with H2-tight systems, ensuring minimal loss and maximum containment reliability.
- Hydrogen is an embrittling gas, capable of damaging materials and affecting their lifespan. Vallourec tackles this challenge by employing optimized hydrogen-resistant metallurgies, safeguarding the integrity of storage materials and prolonging their longevity.
- The flammability and explosivity properties of hydrogen often lead to concerns about storage safety. To address this perception, Vallourec develops storage solutions engineered with high safety-performance, assuring reliability and mitigating potential hazards.
Addressing the unmet need for large-scale storage, current solutions for storing hydrogen prove cumbersome and expensive. For instance:
Overground cylinder racks suffice for storing several kilograms or perhaps a few hundred kilograms of hydrogen, but they become impractical when handling several tons due to space constraints. Geological storage, such as salt caverns or depleted gas reservoirs, offers a cost-competitive approach for storing vast quantities of hydrogen. However, it necessitates suitable geology in proximity and around 5-7 years for construction.
In essence, there exists a market gap for a safe, competitively priced hydrogen storage system that occupies a small footprint, catering to capacities ranging between 1 and 100 tons of compressed hydrogen.
Compressed hydrogen stored in underground pipe assemblies
Safe and secure hydrogen storage in minimal footprint
Occupies up to 30 times less acreage than alternative solutions.
Delphy stores hydrogen underground in a minimal surface footprint offering multiple significant benefits for long-term energy storage. By utilizing existing underground civil works technologies, such as ventilation shafts and access wells, the storage capacity can be maximized without occupying surface lands.
Hydrogen is pressurized and injected into hydrogen-resistant strings, comprised of hydrogen-resistant pipes and hydrogen-tight couplings, creating a reliable and secure storage solution. Delphy’s underground vertical design also minimizes the hazards and reduces set-back distances, compared to above-ground equivalents.
In total, the Delphy occupies up to 30 times less acreage than its above-ground alternatives, typically consisting of racks of cylinders. This stands as a key advantage for project developers, facilitating the integration of hydrogen storage into site layouts and supporting the acceptance and permitting of large-scale hydrogen facilities.
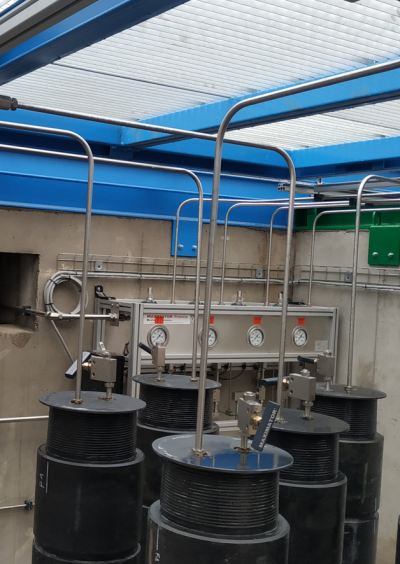

Qualifed technologies for safe, tight & longlasting storage
Available at high pressures up to 500 bar / 7,300 psi.
Ensuring the safe storage of compressed hydrogen is crucial due to its highly flammable and explosive nature. Vallourec’s Delphy storage solution adheres to the highest safety standards.
Drawing upon its proven track record in pipes and connections, bolstered by substantial R&D investment in the hydrogen domain, Vallourec introduces a range of steel materials explicitly engineered and validated for hydrogen applications. This includes qualified hydrogen-resistant tubes and hydrogen-tight couplings. These specialized tubes are designed to withstand hydrogen-induced embrittlement and prevent any potential leakage. Rigorously tested and certified to meet stringent safety standards, they ensure secure containment. The hydrogen-tight couplings guarantee a metal-to-metal seal, minimizing the risk of leakage. By utilizing such materials, the likelihood of hydrogen leaks during storage is significantly diminished, ensuring secure and enduring containment of compressed hydrogen, especially under demanding conditions such as frequent cycling.
Similar dedication has been devoted to validating the entire Delphy storage system architecture, supported by comprehensive risk analysis and qualification plans conducted in collaboration with the esteemed third-party expert, DNV. The ongoing qualification plan includes a demonstration project at Vallourec’s facilities in Aulnoye-Aymeries, serving as a pivotal cornerstone.
Through the vertical storage design and adherence to stringent safety protocols, Vallourec significantly mitigates hazards compared to above-ground solutions. This assertion is validated by modeling risks in Quantitative Risk Assessment and comparing them with surface-based alternatives.
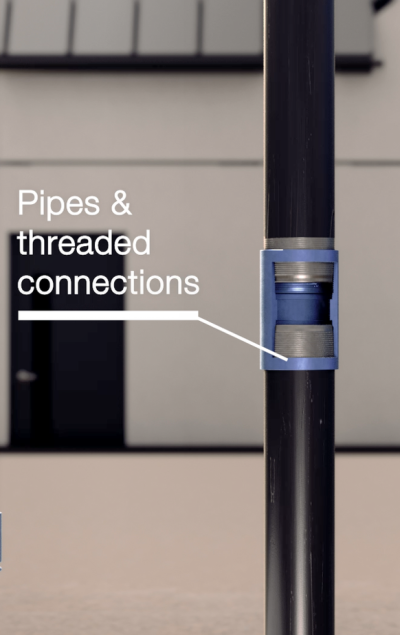
Flexible & modular designs to optimize OPEX & CAPEX
Wide capacity range of 1 to 100 metric tons of H2.
Storing compressed hydrogen in modular and scalable vertical tube strings offers significant advantages that optimize both operational expenditure (OPEX) and capital expenditure (CAPEX) for hydrogen storage projects. Delphy’s project design is fully customizable, adapting to the targeted storage capacity and pressure level, the space available or the optimal depth based on local soil condition.
Additionally, these tube strings provide a scalable solution, allowing for the easy expansion of the hydrogen storage capacity as the project grows. With the ability to add or remove tubes as needed, Delphy can adapt to changing requirements and ensure the efficient utilization of storage space. This modularity also enables cost optimization, as the initial investment is directly proportional to the required storage capacity. By adding more tube strings over time, the project can incrementally increase its capacity, minimizing upfront costs while maintaining flexibility for future expansion.
The vertical arrangement of these tube strings maximizes land usage efficiency, making it an ideal solution for projects with constrained space availability.
In summary, the use of modular and scalable vertical tube strings for compressed hydrogen storage offers a cost-effective, flexible, and efficient solution that aligns with the growth and development of hydrogen projects.
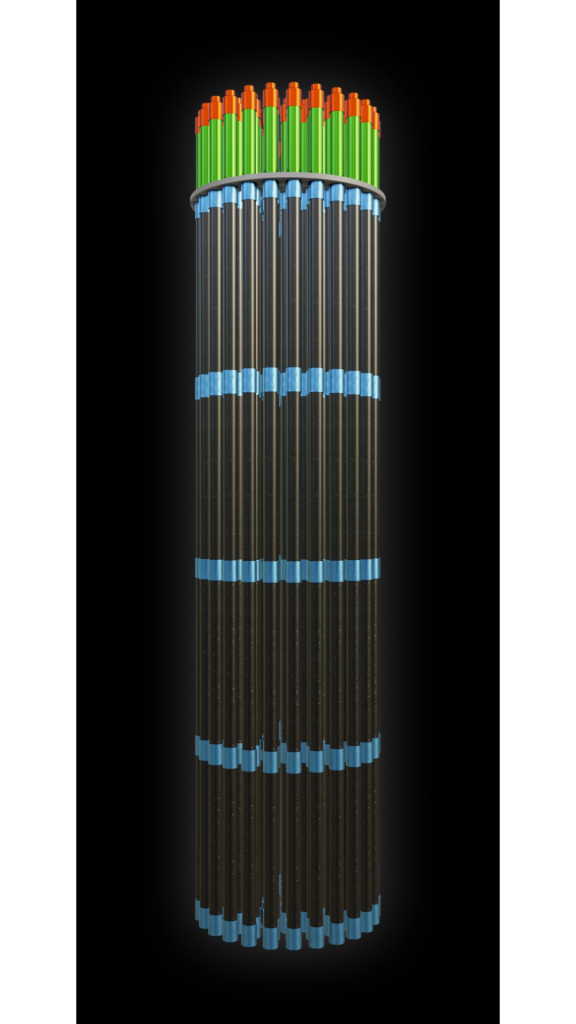
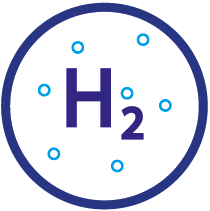
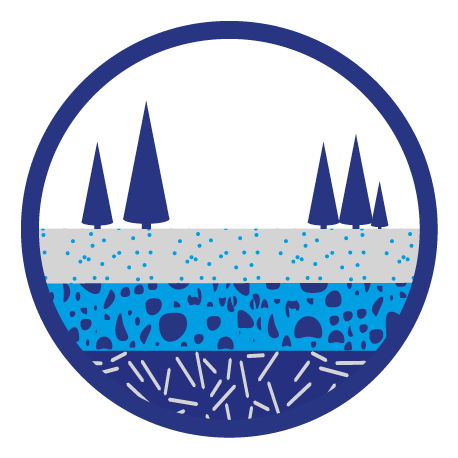
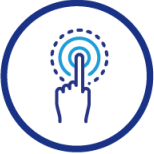
Vallourec announces the official qualification of Delphy, its vertical gaseous hydrogen storage solution, by DNV.
Vallourec is revolutionizing hydrogen storage with its innovative underground vertical system.
By Pierre Martin, Eric Verger, Pierre Mauger, Alvaro Rodriguez, Laurent Boufflers, Anthony Lasjournades, and Nora Brahmi, at Vallourec, presented at the SPE Asia Pacific Oil & Gas Conference and Exhibition in Adelaide, Australia on 17 - 19 October, 2022.
By Florian Thebault and Vincent Designolle, presented at Abu Dhabi International Petroleum Exhibition & Conference (ADIPEC) in Abu Dhabu, UAE in November 2022.
This page contains practical information about the visit to the demonstrator site. The goal of this info pack is to assist our customers and partners in planning their visits to the demo site, in terms of logistics, agenda, itinerary planning, etc.
Watch Delphy’s proof-of-concept construction story
Reach out to us for an in-depth conversation regarding large-scale hydrogen storage for your projects. When is your project slated for? Join us to engage with our experts, discussing your storage requirements and finding the most fitting solutions for your project!
The price of Vallourec’s Delphy large-scale hydrogen storage system is on par or below the price of legacy overground trailer-type hydrogen storage systems. For a formal technical-commercial proposal, please contact your Vallourec representative.
– Quantity of hydrogen stored;
– [Optional] Geographical location, if known;
– [Optional] Inlet and output flow rates, if known;
– [Optional] Output pressure requirements, if any;
1-100 tons.
Vallourec’s Delphy hydrogen storage system stores between 1-100 tons compressed hydrogen in its standard configuration. Customers requiring more than 100t H2 should contact a Vallourec representative for a customized offer.
200-350 barg in standard configuration. Higher pressures are available on request, up to 1,000 barg, for instance for HRS applications.
Up to 100 meters in depth (328ft).
For projects that require construction of multiple wells, there is flexibility to construct wells in a joint-up fashion or separately. The exact configuration of the civil works scope will be determined at the FEED or at the detailed engineering stage. Contact your Vallourec representative for more information.
Twelve (12) months from the Purchase Order date.
The system is delivered in a ‘flange-to-flange’ turn-key configuration. The main component of the scope are:
-Hydrogen-resistant VM110SS pipes and hydrogen-tight VAM® 21 connections;
-Containment cavity up to 100 m deep;
-Auxiliary systems, e.g. piping, control, instrumentation, monitoring, ESD (emergency shutdown) systems;
-Long-Term Service Agreement (LTSA);
20 years.