Additive Manufacturing solutions
This technology utilizes the process of additive manufacturing, which involves constructing a 3D object by adding material in successive layers. As part of the Direct Energy Deposition (DED) process family, WAAM can create shapes that are not achievable through traditional casting or forging and provides short lead times. With its versatility, the technology can cater to a wide range of applications and needs. The company’s material expertise, quality standards, and industrial framework form the foundation of this innovative offering, enabling the delivery of finished and certified parts.
For large metallic components, WAAM is the most promising and fastest 3D printing technology. With it we can design, print and fully qualify metal parts to the highest standards of quality. It offers you greater efficiency and shorter lead times, allowing you to revolutionize how you manage your assets.
How does the 3D printing work?
WAAM uses an electric arc controlled by a robotic arm to melt metal wire directly onto the surface of the base, layer by layer.
How does it impact supply chain?
WAAM does more than create a physical product, it offers the ability to create a digital warehouse so you can cut down physical storage costs and improve your supply chain efficiency by obtaining parts on demand.
How flexible is the process?
WAAM offers the opportunity to shape the part you need in a variety of materials. It provides total freedom to create new designs and new functionalities.
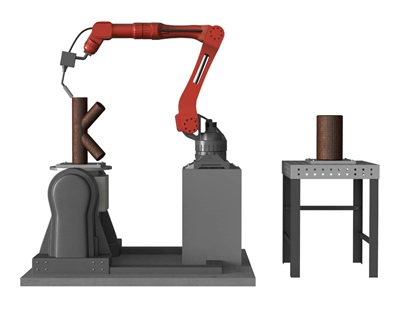
A one-of-a-kind-line
Designed with state-of-the-art technologies (component printing and ultrasonic inspection) capable of manufacture with short lead times (<4weeks).
Integrated
With existing traditional operations to address market requirements.
Printing area of 2m3
L=1m x l=1m x H=2m
A new technology gaining ground
- Carbon steel components are qualified with a pressure test up to 22,500 psi
- Quality plans are available with reference to standards and norms
- New corrosion resistant alloys under qualification in R&D to be available soon
We support your move toward digital warehousing
WAAM radically changes the concept of warehouse logistics. Major O&G companies are increasingly turning to additive manufacturing to improve the agility of their supply chain, to reduce their physical stock and to establish a distributed network of manufactured parts by storing additive manufacturing digital files to be printed upon demand.
Characteristics and typical fields of application
Low yield stress carbon steels for energy, maritime and structural industries. Commonly used for accessories, piping and valves applications currently using grades B, LF2, S355, P265GH, F65…
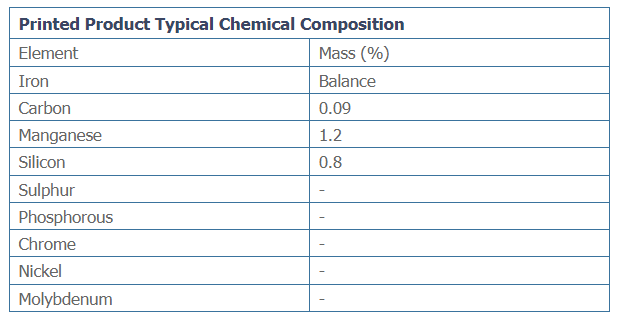
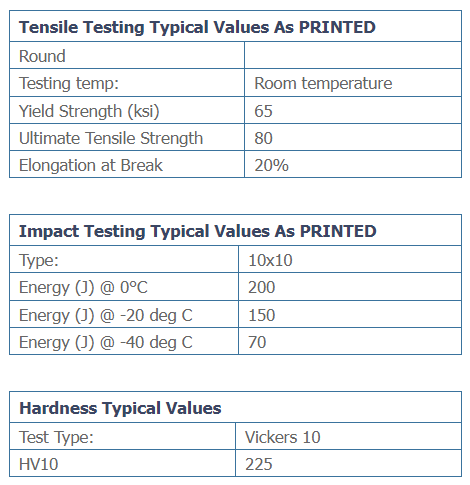
Characteristics and typical fields of application
Versatile high yield stress carbon steels, for a number of applications requiring high mechanical properties in energy, transport and structural industries. Suitable for surface components in O&G such as end fittings, bushings and circulating tools, and structural components in the industry. This material may be considered as a good mechanical alternative to carbon steel material such as 4130, grade 100, S890. Yield strengths from 100 ksi to 120 ksi without heat treatment and 110-140 ksi with heat treatment.
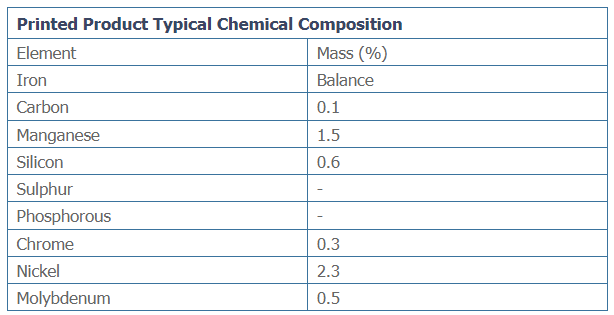
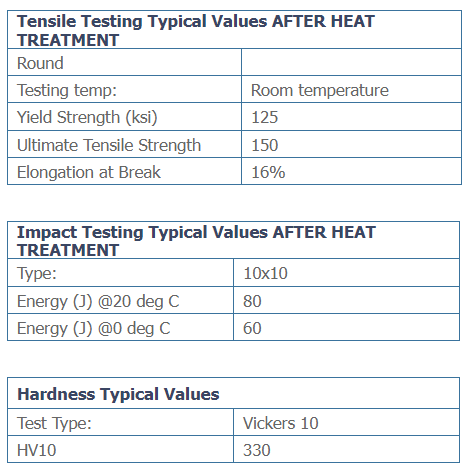
Characteristics and typical fields of application
Covering a very wide range of application for challenging environment for energy, maritime and structural industries using materials such as 316L, F51, X2CrNiMo22-9-3.
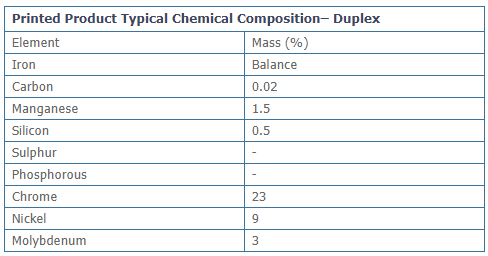
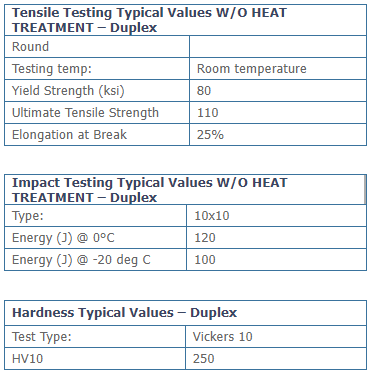
Characteristics and typical fields of application
Covering a very wide range of application for challenging environment for energy, maritime and structural industries such as F6NM, 13/4.
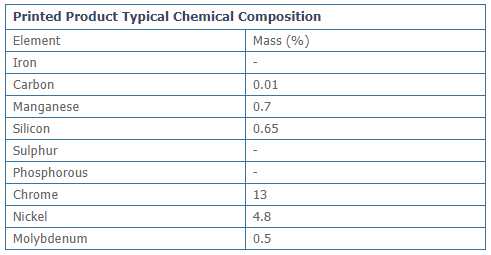

Characteristics and typical fields of application
Nickel based alloys, widely used in aerospace, chemical, petrochemical and marine industries for its superior corrosion resistance properties under various harsh environement including salt water condition. This material has excellent strength from room temperature to elevated temperature. Available production data for 625 material:
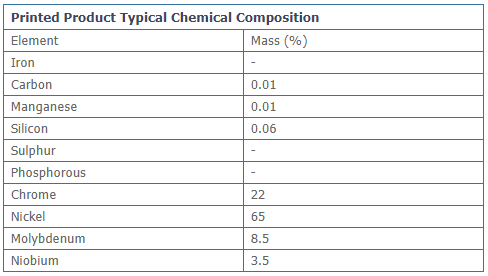
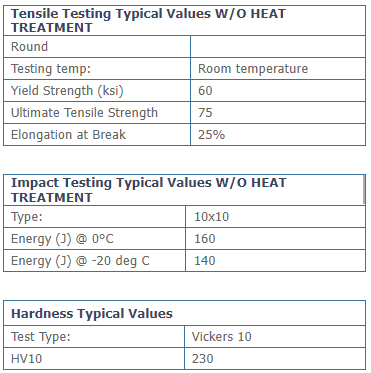
Safety piece for well control
Dimensions: 1072 x 360 x 360 mm
Weight: 236 kg
Grade: X90
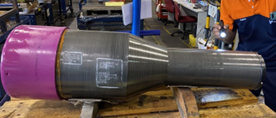
Safety braking hook
Dimensions: 320 x 170 x 50 mm
Weight: 12kg
Grade: X65
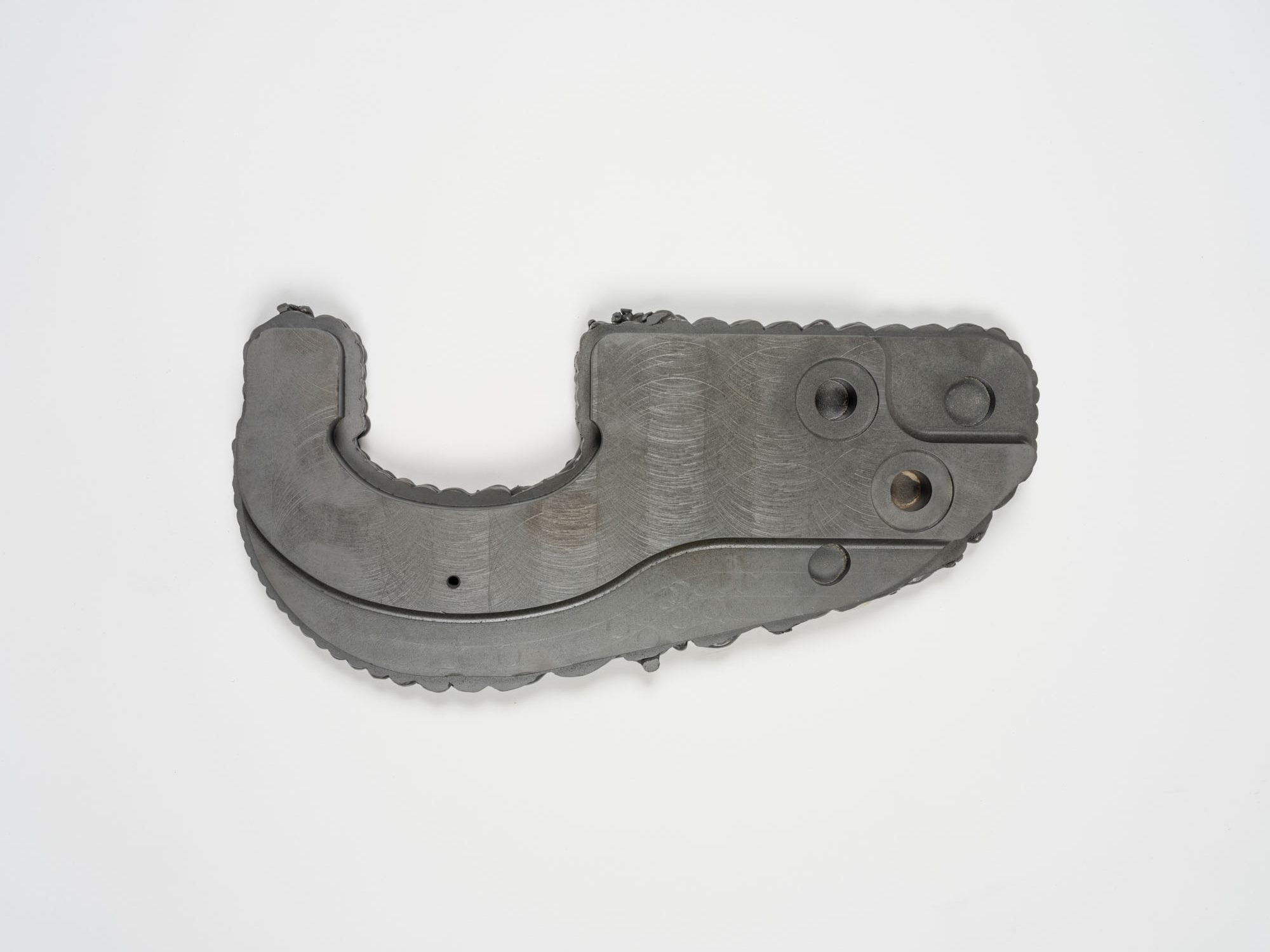
Maintenance part
Dimensions: 280 x 280 x 120 mm
Weight: 17kg
Grade: X65
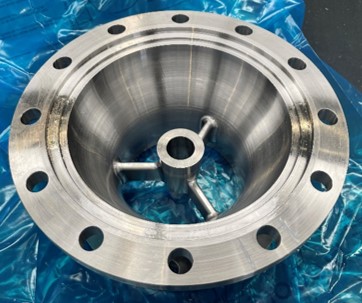
Sealing ring for hydroelectric valve
Dimensions: 900 mm Ø
Weight: 180 kg
Grade: 13Cr-4Ni
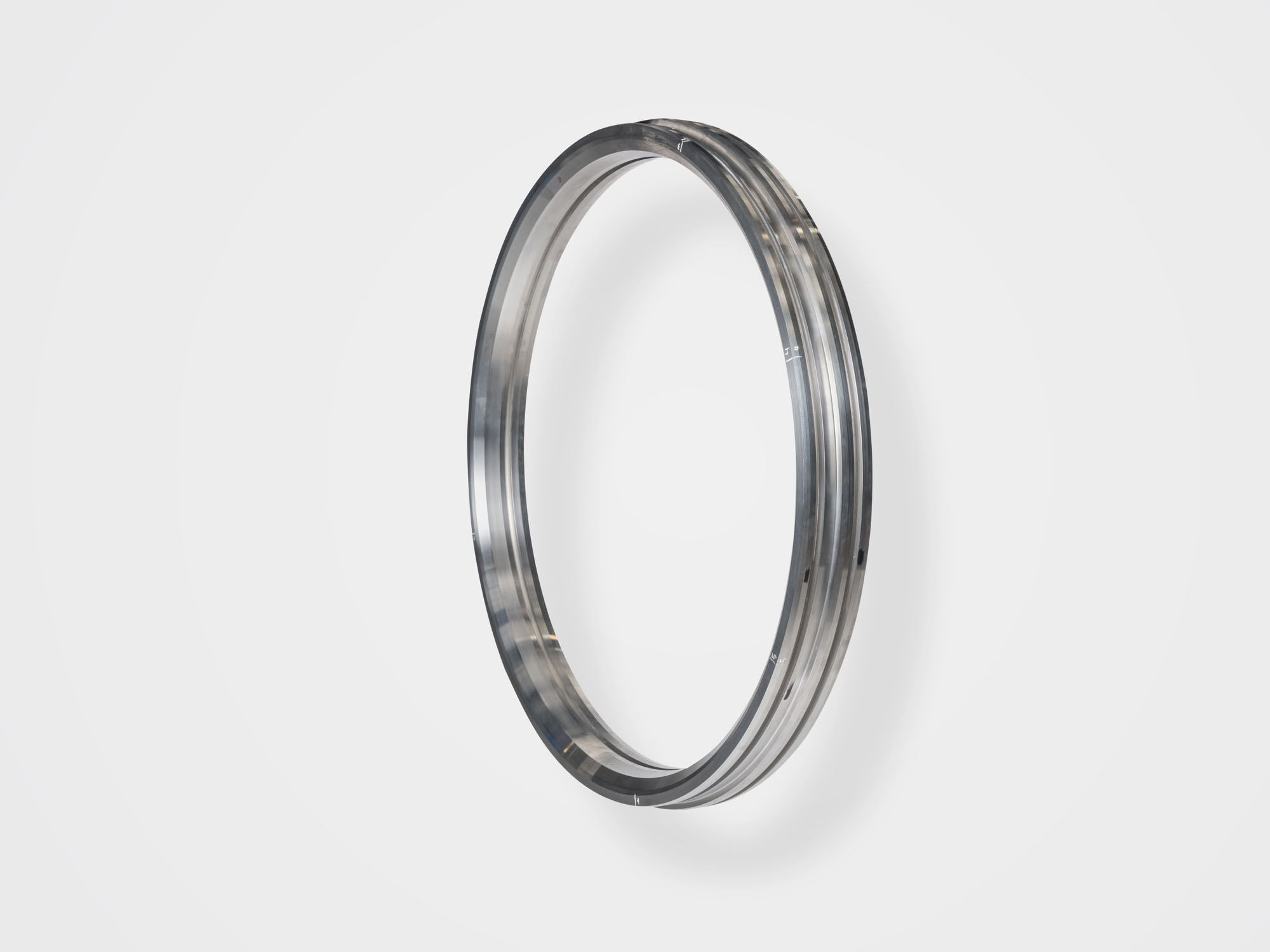
On-stream leak sealing clamp for refineries and petrochemical plants
Dimensions: 700 x 400 mm
Weight: 40 kg
Grade: Carbon steel (Grade B)
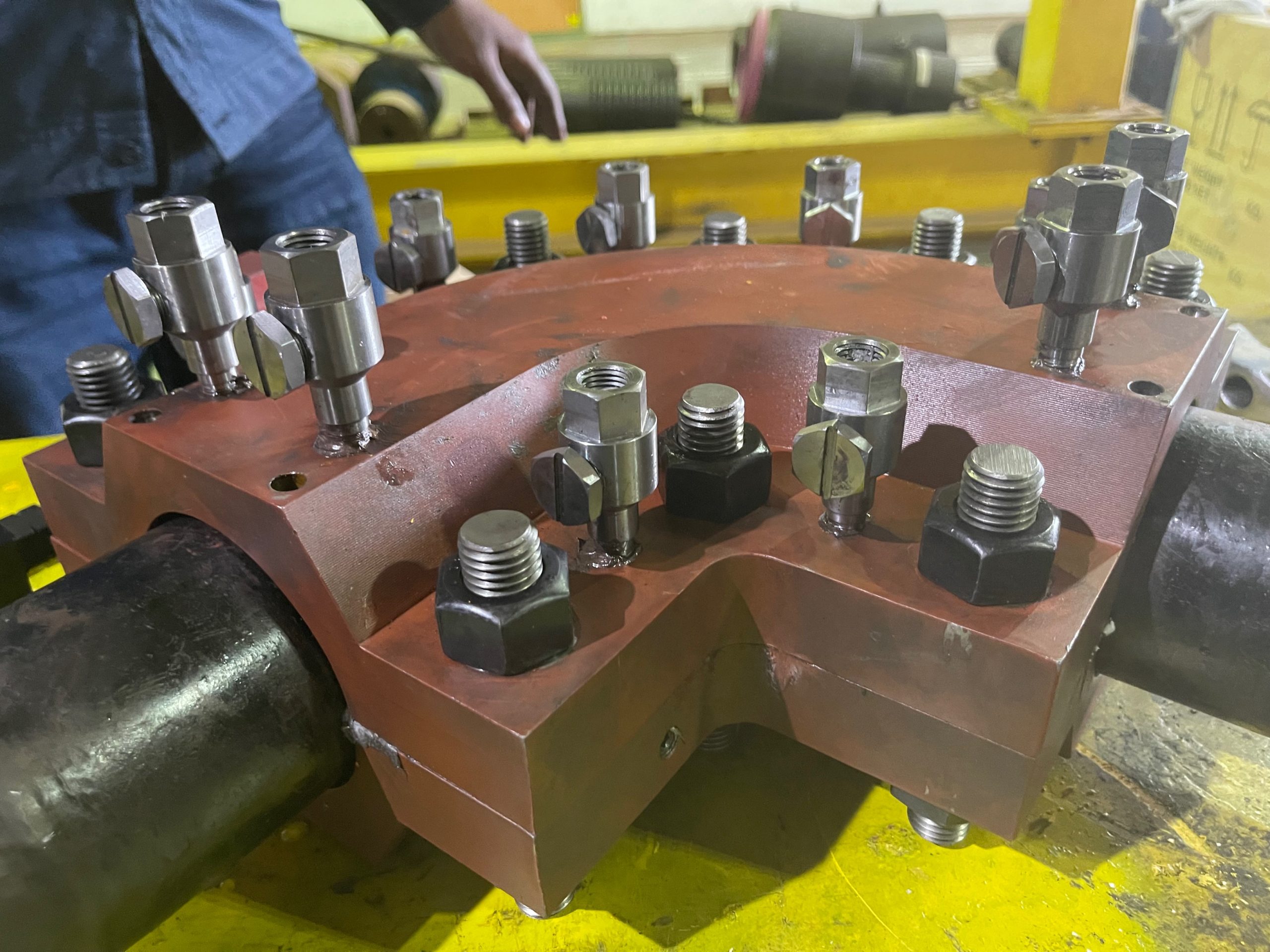
Component used to anchor the pipeline in order to contrast thrust forces.
Dimensions: 2500 x 470 mm
Weight: 330 kg
Grade: X65
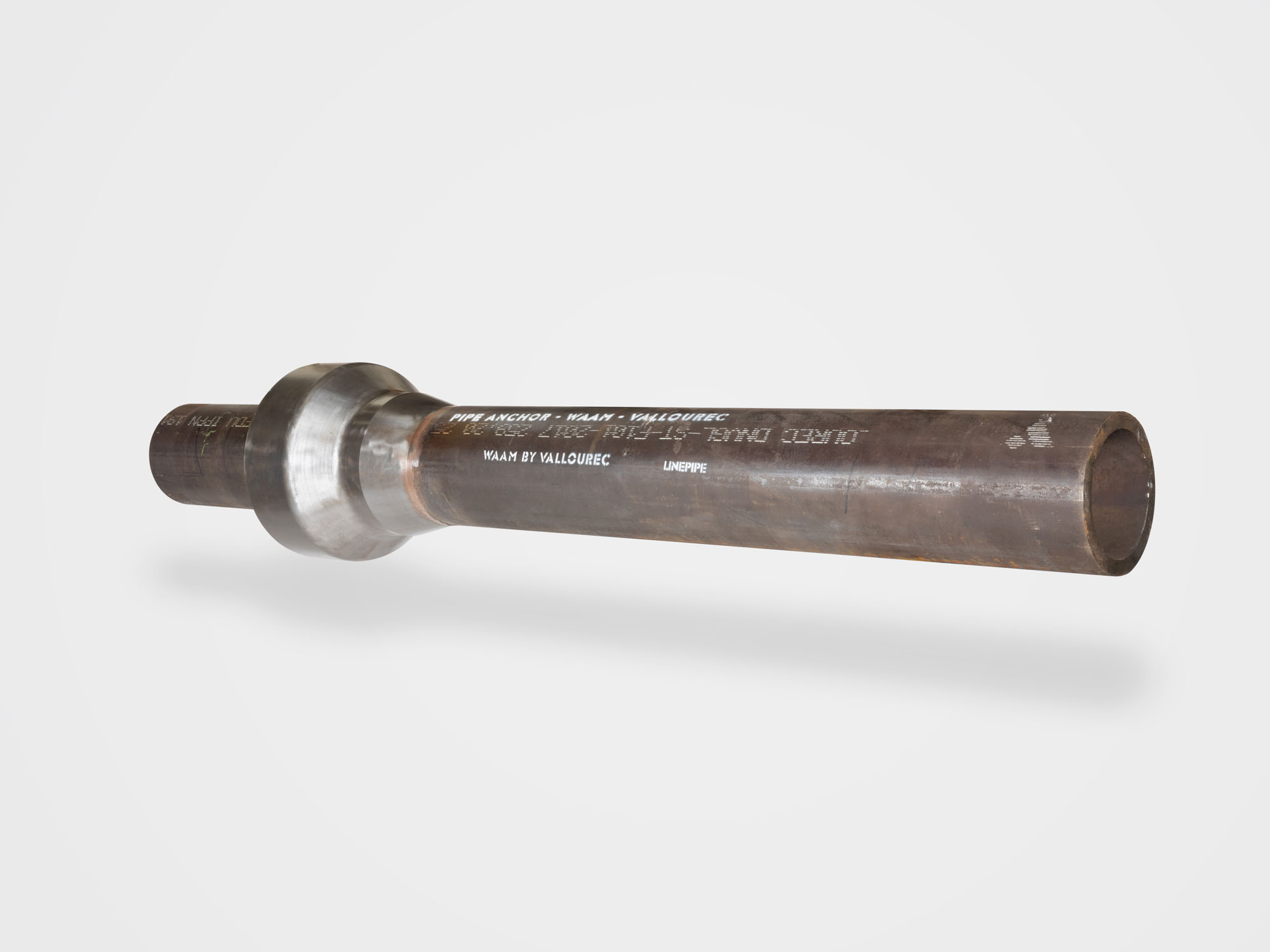
- World Oil Tech Session “Powering Ahead: Using Additive Manufacturing in the Development of Large Metallic Components for O&G”
> View the session now!
- Webcast “Thermal Spray & Wire Arc Additive Manufacturing”
Vallourec has manufactured the first safety-critical sealing ring using Wire Arc Additive Manufacturing for EDF Hydro’s hydroelectric facilities. This component, manufactured in martensitic stainless steel, is 1-meter long in diameter and weighs approximately 100kg. “Today, we have proved the benefits and the process of this technique and now we would like to scale up production and benefit from this new supply method in our facilities, which will involve thousands of components.” Sylvain Guyot, Additive Manufacturing Lead at EDF Hydro.
Discover our OCTG Solutions
More information